Injection Moulding is an adaptable, efficient method of creating plastic parts for a range of applications and industries. Primarily used to produce high volumes of the same product, the process includes turning solids into liquids, and then into a plastic solid form to finish. Injection Moulding requires attention to the specific design restrictions to ensure the benefits and quality standards are met. From the textiles industry to the automotive sector, injection moulding is used in a variety of ways to offer companies a hard-wearing, simple solution.
Advantages Of Injection Moulding
March 4, 2022
By Annie Everill
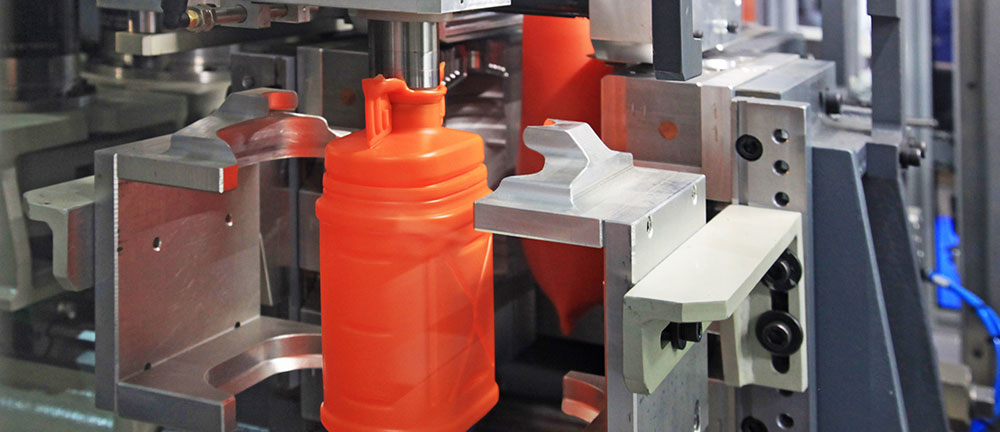
Top Advantages Of Injection Moulding
High production efficiency
Offering a speedy production process, injection moulding has a much quicker output rate compared to the other methods. Although the speed of production is reliant on the size and complexity of the goods, the time passed between each cycle time is kept to a minimum. This is beneficial for companies wanting high volumes of products in a short space of time whilst also increasing revenue and profits.
Flexibility of design
When creating and choosing the plastics for a project, aspects such as material, colour and shape are just some of the essential factors to consider. Thanks to the development of polymers and resins, the possibilities are endless through colour systems and techniques. Choosing the right resins will come down to the impact strength, tensile strength, water and heat absorbency plus elasticity.
Enhanced strength
Before forming the product, it’s important to consider the function and purpose of its final form. This will alter how strong the material needs to be. Deciding if the part needs to be flexible or rigid should be one of the first thoughts before manufacture. If the goods need to have high strength, injection moulding has the power to deliver.
Complex design
A large bonus with injection moulding is the ability to handle complex parts with the idea of making multiple, even better. For a successful moulding process, the initial design has to be developed to maximise efficiency and meet all quality requirements. Some of the design elements to consider include thickness, rib, weld lines, gates and vents.
Waste production
Compared to systems such as CNC, injection moulding is a much less wasteful process and is constantly improving in the ethical sense. Producing less post-production scrap, the positive thing about the waste that is made is the ability to recycle and reuse.
Low labour costs
Due to injection moulding being an automated process, only a sole operator is needed to control and manage the system. With the units working through the power of robots and machinery, automation helps to reduce both the manufacturing and labour costs.
Product consistency
Operating as a repeat process has its perks. Injection moulding offers the reliability that each product is going to look the same and doesn’t require any alterations. This factor is the reason why the design process is so crucial as this is how each and every product will look.
No finishing requirements
There is normally no to very little post-production work required.
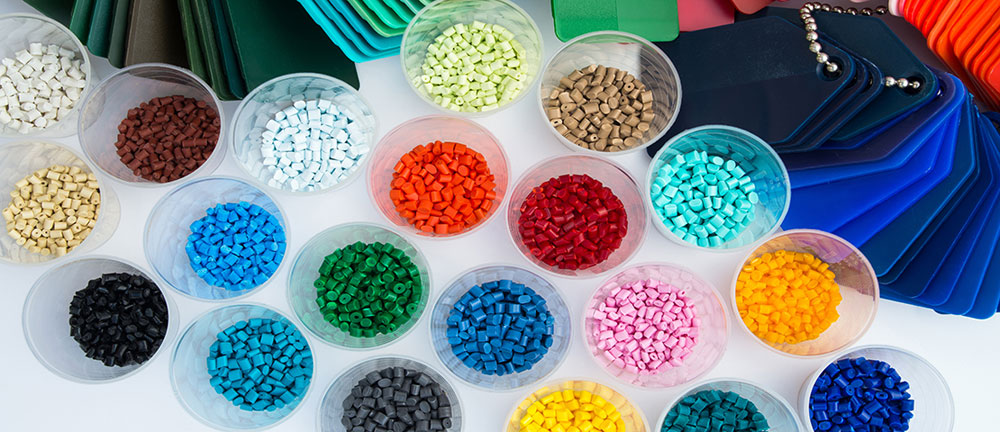
Who Uses Injection Moulding?
The injection moulding process and the goods made from it can be found all over the world in many different environments. Used for different purposes and adapted in specific ways, this versatile method brings all kinds of opportunities and benefits with just a few drawbacks.
The packaging industry
Mostly referring to the food and drink industry, injection moulding is used in the production of wraps, protective layers, trays and boxes. Popular due to the lightweight and hygienic finish, it is also a good material for point of sale and advertising.
Healthcare
Due to plastics’ resistance to bacteria, this material is used on a great scale in medical and healthcare products. Offering easy wipe surfaces, some examples may be syringes, bottles, tubs, PPE, petr dishes and vials.
Textiles
Used for both aesthetic and functional purposes, injection moulding is a key process used in the textile industry. Ranging from sunglasses to twines, the benefits include colour fastness, UV ray protection, anti bacteria damage and waterproof coverage.
Automotive, transport and logistics
Typically found in cars, vans and lorries, injection moulding can be used for larger scale transport such as boats and aeroplanes. Used in the manufacture of bumpers, handles, dashboards, air vents and storage, plastic can also be found in the engine.
Electronics
Used in a multitude of different applications, injection moulding offers a highly bespoke specification with a range of finishings. Offering benefits such as colouring and insulation, electronic companies use injection moulding for phones, tablets, circuits and charging devices.
Construction
Ranging from large to small projects, the construction industry uses this process for heavy duty machinery, fixtures, fittings, toolmaking and moulds. The moulding process can also be used for protective equipment such as sign posts to machine guards.