Rapid prototyping is a process used to develop products at a fast rate, creating both a physical and digital model of the piece or design. This method involves specialised tools and technologies which efficiently create a basic prototype which can later undergo improvements and changes. Designers, developers and engineers use rapid prototyping for a quick solution for testing new ideas. They will then identify faults and determine potential issues during production. The techniques used can vary depending on the final product or design and include methods such as 3D printing, CAD/CAM or virtual reality.
Rapid prototyping: What is it and how does it work?
April 4, 2023
By Annie Everill
What is rapid prototyping?
How does rapid prototyping work?
A variety of manufacturing technologies are used for rapid prototyping including machining, casting, moulding and extruding. It is also essential to understand the types of prototypes which are categorised depending on the level of accuracy required. Accuracy can vary from low-fidelity which is recognised as simple, quick testing that is focused on the broader concept, to high-fidelity. Prototypes that appear and function similarly to how the final product would.
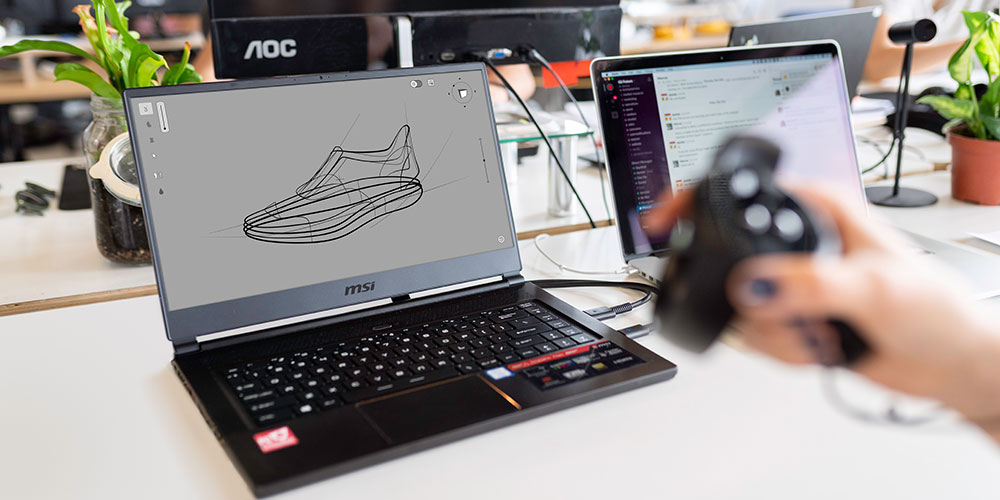
The process of rapid prototyping
Design
No matter the industry, the first step is to create a digital design of a product or part, typically using computer-aided design softwares. These modern softwares allow designers to create 3D imagery and models which show a unique sense of detail and accuracy. The design stage typically starts with simple sketches and ideas and turns into a digital file which can be viewed easily by both parties involved.
Preparation
Once the design is complete and has been confirmed, the next step is all about preparation. This step includes tasks such as preparing CAD files, setting up machinery or creating any necessary equipment needed during the process.
Creating a prototype
Once the design and preparations are complete, the prototype can be created. Using methods such as 3D printing, CNC or injection moulding, the prototype process is all about completing a model efficiently and accurately. For items such as toolmaking, this stage is crucial to ensure the item is customer friendly, comfortable to use and practical.
Tests and evaluations
The primary point of a prototype is to have a product that can be evaluated and examined before the real thing is produced. This feedback can be used to edit the design, functionality or specific parts and is one of the most important stages. At this stage, designers and engineers will find ways they can improve the product and make any necessary changes.
Modification
Based on the results of the evaluation, modifications will be carried out, ranging from the initial design to a physical imperfection. The prototype will be recreated in line with these modifications and the process will repeat itself until the manufacturer is satisfied with the final outcome. The product will also need to meet all requirements and quality standards and will be delivered by hand or automation.
“Rapid prototyping has a number of advantages for manufacturers as they can support the wave of new product companies adopting digital transformation. By leveraging the flexibility of smart manufacturing for rapid prototyping, manufacturers can offer design and engineering teams the means to iterate quickly and test with agility. Improving on an initial concept prototype through to fully functioning prototyping on a digital thread for design to production is possible today, this can minimise waste and cost and drastically reduce failures when scaling out to mass production. This also becomes attractive for manufacturers to empower product companies in new innovation methodologies that can engage customer feedback every step of the way. ”
Christina Rebel, Co-founder & Chief Growth Officer, Wikifactory
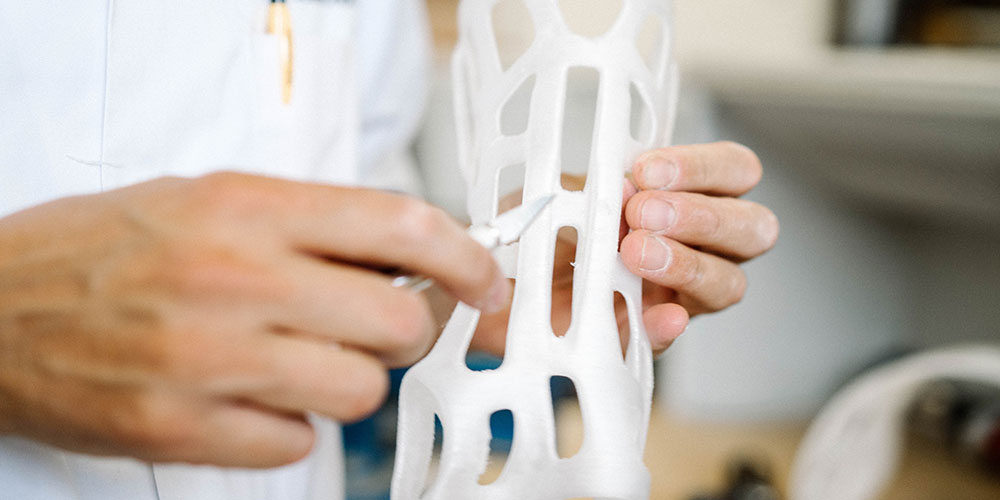
Advantages and disadvantages of rapid prototyping
This fairly new but popular method is used by engineers and manufacturers worldwide and comes with several advantages, helping with product development, cost and time efficiency. Here are some of the main advantages that rapid prototyping offers.
Advantages
Quicker production: The whole idea of the process being rapid is its main benefit. Allowing for quicker design alterations and efficient results, rapid prototyping is a key way to move production forward at a quicker rate.
Lower costs: Through the testing process, potential quality issues and mistakes can be identified, reducing the cost of product defects or delays.
Quality control: Similarly, the testing and evaluation stage also helps designers and manufacturers identify quality-related issues before the final product is released.
Workplace collaboration: As rapid prototyping involves new softwares, this enables more effective collaboration between designers, developers and the final customer. The results are easily accessible and shared through digital formats and enable clear communication.
Innovation: Computer-aided design and all the softwares available have given designers greater freedom in what they can design. Moving away from traditional, static 2D designing, designers are given greater freedom and inspiration.
Disadvantages
Some of the disadvantages involved in rapid prototyping involve high initial costs and environmental concerns. Let’s take a deeper look into the drawbacks of rapid prototyping.
- High initial costs
- Limited material options
- Not scalable for large-scale production
- The prototype is not always accurate to the final product
- Environment and waste material